
The skateboard chassis is made of submarine-grade steel, aerospace-grade aluminum alloy, and multiple barrier structures to enhance rigidity.
December 26, 2024 10:50
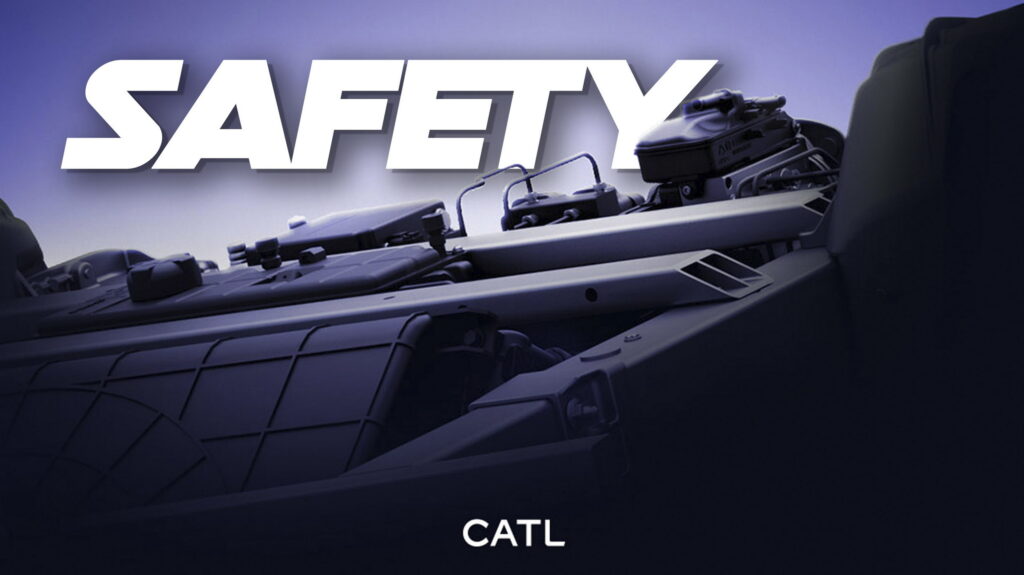
- CATL’s new Bedrock chassis was unveiled in China, setting a new standard for battery safety.
- The chassis of the electric skateboard adopts a modular design, which shortens the research and development cycle.
- Avatr will be the first automaker to use the new skateboard chassis in a production model.
Battery giant CATL has launched a new electric vehicle skateboard chassis focused on providing maximum safety for the battery pack. The CATL bedrock chassis survived a 120 km/h (75 mph) frontal collision without catching fire or exploding, setting (according to the company) a new standard for the safety of future electric vehicles.
The skateboard chassis integrates batteries and adopts a “three-dimensional bionic tortoise shell structure” and a “high-stretch energy-absorbing heat insulation film.” For its structure, CATL used submarine-grade hot-formed steel, aircraft-grade aluminum alloy and multiple barrier structures to make it as strong as possible.
More: See what happens when two cars hit a Chinese electric car at 60km/h in triple crash test
In addition, the battery’s high-voltage circuit was disconnected within 0.01 seconds after impact and completed discharge within 0.2 seconds.
Exceed C-NCAP requirements
Thanks to its design, the Bedrock chassis is able to absorb 85% of a vehicle’s collision energy, a significant improvement compared to 60% for conventional chassis. This is important for demanding crashes such as frontal pole crash tests that simulate impacts with trees, utility poles, or animals.
According to CATL, the 120 km/h (75 mph) pole crash test produced increased energy compared to the current C-NCAP standard 56 km/h (35 mph) full-width frontal crash test. 21 times. China New Car Assessment Program).
In addition to the 120 km/h (75 mph) test, the battery cells were also subjected to a high-speed sled impact test of 60 km/h (37 mph), a 90-degree bend test and a saw cut test, proving their resistance to fire or Fire resistance. explode.
Ningde era
Modular design greatly shortens development time
The company claims that the Bedrock chassis shortens the development cycle for new production models from 36 months to just 12-18 months. This is achieved through its modular design, with the chassis separated from the upper body, allowing use in a variety of vehicle types. In addition, the platform is compatible with L3 and L4 autonomous driving and has flexible software.
CATL has confirmed that the Avatr will be the first car manufacturer to use the Bedrock chassis in a production vehicle, but they have yet to reveal when it will be launched.
In a recent video shared on YouTube, CATL explained the steps they take to ensure the safety of their battery packs in a variety of different crashes. The company acknowledges the additional risk of side impacts, so they have improved the design of the battery housing.
Leave a Reply Cancel reply
You must be logged in to post a comment.