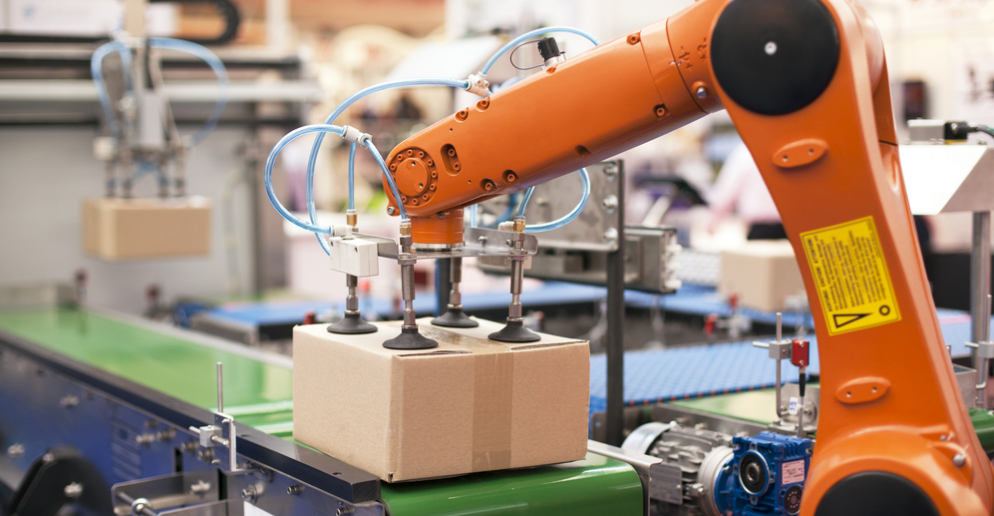
Many warehouse automation systems are powered by the pneumatic energy of compressed air. They are commonly found in shoe sorters, which use air cylinders to actuate switch blocks. They are also common in narrow-belt accumulation conveyors.
Also read: Top 5 Cheap Warehouse Automation Solutions
At first glance, pneumatics appear to be a simple and low-cost solution. There is nothing fancy or magical about the technology. Parts are inexpensive and easy to find. Even if you can’t get the exact same valve from the original manufacturer, any supplier that sells similar parts will be able to provide a suitable part. Troubleshooting is also easy, at least in theory.
However, in practice, the complexity of pneumatic systems makes them highly inefficient and can fail in a variety of ways.
Let’s vent some frustrations
Pneumatic systems are complex and require a large number of parts. This makes them difficult to install and inefficient to operate. Estimates vary, but some believe that pneumatic equipment only effectively utilizes about 5% to 10% of the energy required to operate.
Most of the energy goes into driving the compressor that pressurizes the air. These units are usually located outside or away from the equipment they operate. They generate a lot of noise and heat, so no one wants to work near them. If you are installing a large system, or plan to expand your system later, you need to make sure your compressor is powerful enough to provide the required airflow.
Regular maintenance and care of compressors is essential to keep the air clean and dry. Unfortunately, they are also very expensive. As a result, many operations are conducted with degraded air quality. Over time, dust accumulates inside cylinders and valves, causing a decrease in system efficiency, energy, and speed.
Compressor failure obviously means costly unplanned downtime, but even a tiny air leak can bring down your entire system. If you’ve ever tried to drink from a broken straw, you’ve experienced a similar problem. Now imagine that straw is several miles long, snaking its way throughout your warehouse and branching off in multiple directions. A leak anywhere in that line could cause a loss of airflow throughout your entire system—and you have no idea where it is.
Pressurized air also makes a loud noise, like the sound you hear when a kneeling bus lowers to make it easier for passengers to get on. Although some cylinders have parts designed to reduce the noise, they are still very noisy. You will hear this noise every time you start it.
Technological disadvantages put downward pressure on your business
Air systems do not provide speed or position control. While most pneumatics have an end-of-line switch that tells you if the cylinder has extended, you have no way of knowing what happened between the start and end of the motion. This means that if the performance of the cylinder degrades, there is no early warning. You won’t know there is a problem until the cylinder breaks, which can cause unplanned downtime.
Pneumatics are also slow compared to other technologies. The only way to increase cylinder speed is to increase airflow. The upper limit of what can be achieved this way is usually much lower than electric actuation. This has become a problem to some extent, as distribution centers are under more pressure than ever to increase throughput.
Are electric alternatives the answer?
Electric solutions offer many advantages over pneumatic solutions, including easier installation and maintenance, superior performance, quieter operation, and greater reliability. They also make it easier for you to expand at your own pace.
For example, adding a new conveyor to a pneumatic system typically requires a larger compressor as well as all new air lines. In contrast, expanding an existing electric system is more likely to be a “plug and play” operation. You can install new equipment with little to no additional infrastructure. Plus, you can start small without having to worry about oversizing the compressor to support future upgrades.
Let’s review the pros and cons of three electric alternatives to pneumatics: solenoid valves, servomotors, and Solligence™ fast-rotation actuators.
Solenoid
Solenoids offer fast start-up times and a good balance of performance and cost. Solenoids are small, inexpensive, and low maintenance, typically requiring only a pair of cables. If they fail, they can be replaced quickly with minimal cost and downtime.
Like a cylinder, a solenoid has no speed or position control. If you want to know what it is doing, you need to put a sensor somewhere.
The solenoid also needs to be managed by an external controller and requires a large power supply to achieve higher speeds. The power supply needs to be sized optimally to provide the right burst of energy. Too little power and the solenoid will not operate at the required speed. Too much power and it may burn out the device.
Servo Motor
Servo motors in warehouse automation are a lot like sports cars. They are the fastest solution on the market, allowing precise control of speed and position. Built-in encoders provide visibility and intelligent feedback.
However, like sports cars, servo motors and their drives are expensive. They require high-power power supplies, complex software, and are complicated to configure. These disadvantages combine to make them cost-prohibitive for most warehouse applications.
Solligence Fast Rotary Actuator
Johnson Electric developed Solligence to incorporate many technologies previously available only in servo motors into a simple solenoid valve. This combination overcomes the shortcomings of both options (and long-standing industry performance limitations) while simplifying installation and reducing operating costs.
The integrated drive unit eliminates the need for external drivers, control boxes, and assembly labor. Low voltage and current requirements reduce installation and energy costs, allowing the use of narrower wires and smaller, less expensive power supplies. Integrated onboard energy storage allows power to be slowly “drawn” from the main bus throughout the cycle, driving the solenoid in bursts of power to produce high speeds as needed.
Solligence continuously monitors changes in motion duration, adjusting drive configuration as needed to continue to meet specifications. The unit also triggers an alarm when wear is detected, preventing costly, unplanned downtime.
Weighing the pros and cons
While low capital costs continue to make pneumatic systems popular, the operating and maintenance costs of these inefficient systems can quickly outweigh your initial savings. So it’s no surprise that more and more of the world’s leading logistics companies are turning to electric alternatives. They’re ready to move away from the downtime risks, operating costs, and other hassles of pneumatic systems.
Whether you choose a traditional solenoid or the innovative Solligence fast-turn actuator, electric alternatives offer cost and performance advantages that pneumatics can’t match. You’ll benefit from faster, more reliable automation without the frustration.
Leave a Reply Cancel reply
You must be logged in to post a comment.